Table of Contents
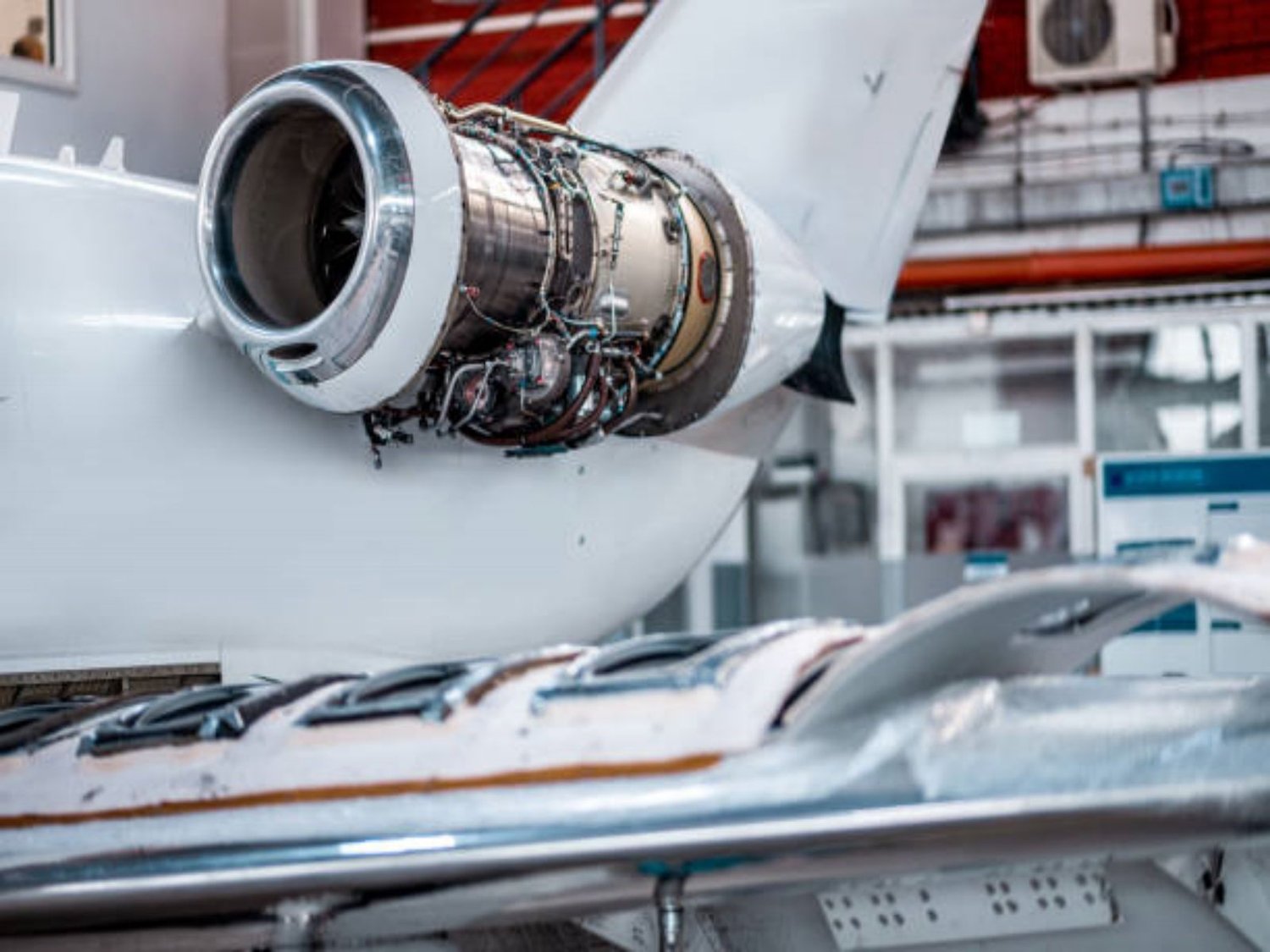
From Raw Material to Flight-Worthy: The Journey of Titanium in Aviation Production
Titanium, a lightweight and durable metal, has become a crucial material in the aviation industry. Its exceptional strength-to-weight ratio and resistance to corrosion make it ideal for various aircraft components. In this article, we will take a closer look at the fascinating journey of titanium, from its raw material form to being transformed into flight-worthy parts for aviation production.
The Discovery of Titanium
Titanium was first discovered in 1791 by British clergyman and mineralogist William Gregor. He found a black, magnetic sand that contained a new element, which he named "manaccanite." It wasn't until 1795 that German chemist Martin Heinrich Klaproth independently identified the element and named it "titanium" after the Titans of Greek mythology.
Extraction and Refining
The extraction and refining process of titanium begins with the mining of titanium ore, primarily found in beach sands and igneous rocks. The most common form of titanium ore is ilmenite, which contains iron and titanium dioxide. After being mined, the ore undergoes several steps of processing, including crushing, grinding, and magnetic separation, to obtain pure titanium dioxide.
Conversion to Titanium Sponge
The next step in the journey of titanium is the conversion of titanium dioxide into titanium sponge. This is achieved through a process called the Kroll process, developed by American metallurgist William J. Kroll in the 1940s. In this process, titanium dioxide is reacted with chlorine to produce titanium tetrachloride. The titanium tetrachloride is then reduced with molten magnesium, resulting in the formation of titanium sponge. The titanium sponge is a porous, metallic form of titanium that serves as the precursor for various titanium products.
Melting and Casting
Once the titanium sponge is obtained, it is then melted and cast into ingots or billets. The melting process involves heating the titanium sponge in a vacuum or controlled atmosphere furnace until it reaches its melting point. The molten titanium is then poured into molds to form ingots or billets, which are solidified and later used for further processing.
Forming and Machining
After the casting process, the titanium ingots or billets are formed into the desired shape through various techniques such as forging, rolling, or extrusion. These forming processes help refine the microstructure of the titanium and improve its mechanical properties. Once the desired shape is achieved, the titanium undergoes machining processes such as milling, turning, and drilling to create precise dimensions and smooth surfaces.
Heat Treatment
Heat treatment is a crucial step in the journey of titanium as it helps enhance its mechanical properties. The titanium parts are heated to specific temperatures and held for a certain duration to achieve desired changes in the microstructure. This process can improve the strength, hardness, and ductility of the titanium, making it suitable for aviation applications that require high-performance materials.
Surface Treatment and Coating
To further enhance the durability and corrosion resistance of titanium parts, they often undergo surface treatment and coating processes. Surface treatments such as anodizing or chemical etching create a protective oxide layer on the surface of the titanium, preventing corrosion and improving its appearance. Additionally, coatings like paint or ceramic coatings can be applied to provide additional protection against wear, abrasion, and extreme temperatures.
Quality Control and Testing
Before titanium parts can be deemed flight-worthy, they must undergo rigorous quality control and testing procedures. These tests include non-destructive testing methods such as visual inspection, ultrasonic testing, and X-ray inspection to ensure there are no defects or imperfections in the titanium parts. Mechanical testing, such as tensile and fatigue testing, is also conducted to verify the strength and durability of the titanium components.
Integration into Aviation Production
Once the titanium parts pass all quality control tests, they are ready to be integrated into aviation production. Titanium is used in various aircraft components, including airframes, landing gears, turbine blades, and engine components. Its lightweight nature contributes to fuel efficiency and reduces the overall weight of the aircraft, while its strength ensures the structural integrity and safety of the aircraft.
Conclusion
From its discovery to its transformation into flight-worthy parts, the journey of titanium in aviation production is a remarkable process. The extraction, refining, conversion, and manufacturing stages all contribute to creating a high-performance material that revolutionizes the aviation industry. Titanium's exceptional properties make it an indispensable material for modern aircraft, enabling safer, more efficient, and reliable air travel.