Table of Contents
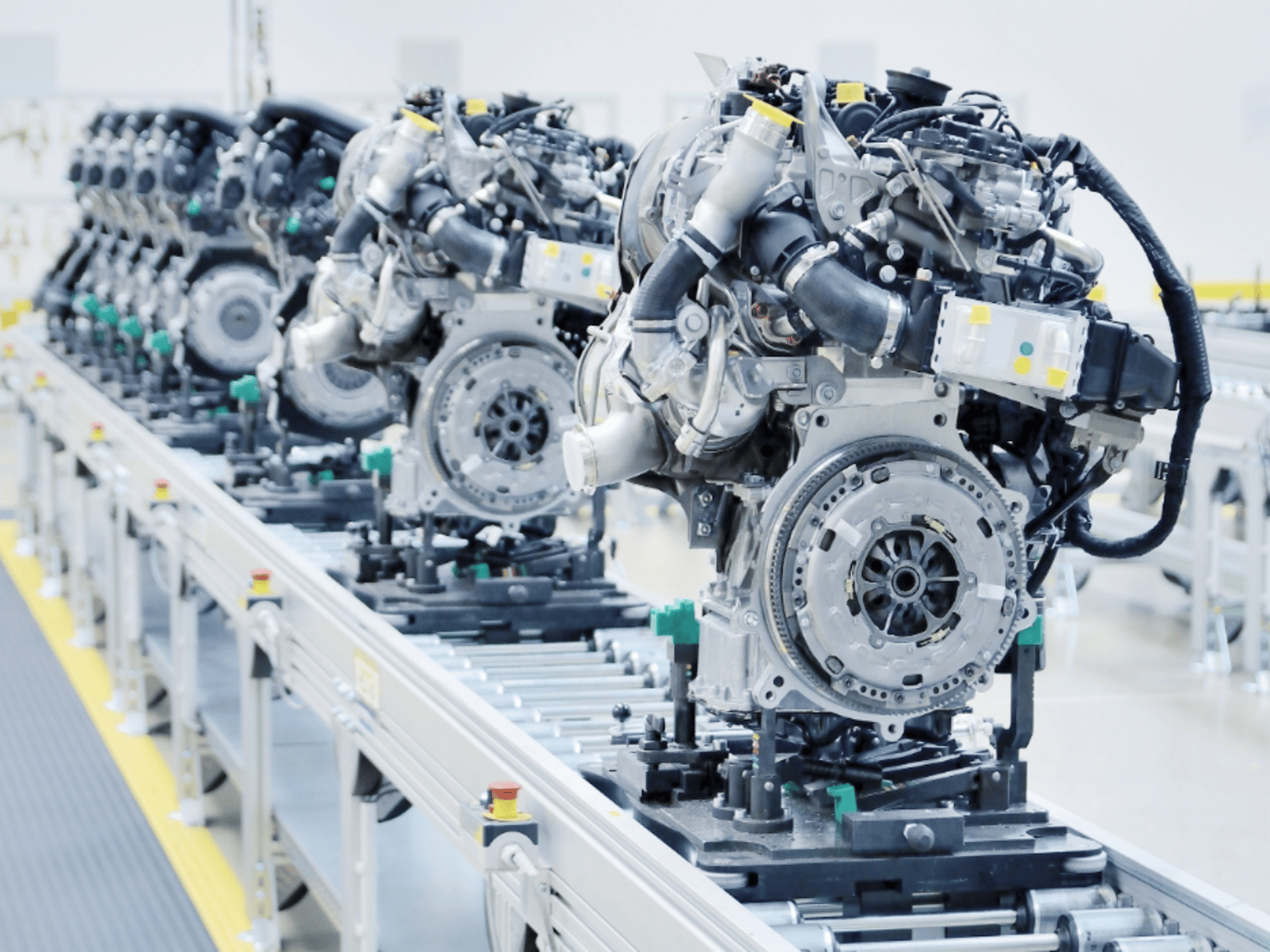
Titanium, renowned for its strength, durability, and lightweight properties, has emerged as a transformative element in various industries, particularly revolutionizing engine innovation. This exceptional metal has played a crucial role in reshaping the design and manufacturing of engines, resulting in heightened performance and efficiency.
Exploring Titanium's Role in Car Engine Production:
The Historical Footprint of Titanium in Engine Innovation: The utilization of titanium in engine construction dates back to the mid-20th century when engineers and scientists recognized its extraordinary properties. Initially embraced by the aerospace industry for its high strength, resistance to extreme temperatures, and corrosion resistance, titanium gradually made its way into automotive engines. Early adoption was primarily in high-performance racing engines due to cost and manufacturing challenges. However, advancements in production techniques and increased availability have made titanium more accessible to mainstream automotive manufacturers.
Today, the collaboration between engine manufacturers and titanium ground bar suppliers, such as STA in China, enables the production of various engine components. These include valves, connecting rods, pistons, and exhaust systems. The lightweight nature of titanium ground bars contributes to reduced engine weight, leading to improved fuel efficiency and overall performance.
Advantages of Titanium in Engines: The incorporation of titanium in engine design brings forth several advantages that significantly enhance performance and efficiency. First and foremost, titanium's exceptional strength-to-weight ratio reduces the overall engine weight, translating into enhanced fuel efficiency. The lightweight attribute also contributes to improved weight distribution, enhancing handling and maneuverability.
An additional notable advantage lies in titanium's outstanding resistance to corrosion. This resistance ensures the longevity and reliability of engine components exposed to high temperatures and harsh environments, reducing maintenance costs and extending the engine's lifespan.
Furthermore, when processed by a reputable titanium ground bar supplier like STA, titanium exhibits excellent heat resistance. This makes it ideal for components subjected to extreme temperatures, such as exhaust systems and turbine blades. The material's ability to withstand high temperatures without deformation ensures optimal engine performance even under demanding conditions.
Titanium Alloys and Their Automotive Applications:
Utilization of Titanium Alloys in Automotive Engineering: While pure titanium possesses remarkable properties, alloying it with other metals further enhances its characteristics. Titanium alloys offer a spectrum of mechanical properties, allowing engineers to tailor the material to specific application requirements. In the automotive industry, titanium alloys find extensive use in critical engine components where strength, durability, and heat resistance are paramount.
One prominent titanium alloy in the automotive sector is Ti-6Al-4V, also known as Grade 5 titanium. Combining titanium with aluminum and vanadium, this alloy delivers excellent strength, low density, and exceptional heat resistance. Ti-6Al-4V is commonly employed in valves, connecting rods, and turbocharger impellers, contributing to improved engine performance.
Another notable titanium alloy is Ti-3Al-2.5V, striking a balance between strength, ductility, and formability. Widely used in applications requiring complex shapes, such as exhaust systems and intake manifolds, this alloy's excellent weldability and corrosion resistance make it an attractive choice in automotive engineering.
Sustainability and Environmental Impact:
Titanium's Environmental Contribution in Engine Manufacturing: In terms of sustainability, titanium holds several advantages over traditional metals used in engine manufacturing. The lightweight nature of titanium contributes to reduced fuel consumption, aligning with the industry's goals of lowering carbon emissions. This attribute becomes increasingly significant in the context of environmental sustainability.
Moreover, titanium's exceptional corrosion resistance ensures the longevity of engine components, reducing the need for frequent replacements. This not only saves costs but also minimizes the environmental impact associated with the disposal and manufacturing of new components. Additionally, titanium is fully recyclable, positioning it as a sustainable choice for engine manufacturing.
In Search of a Titanium Ground Bar Supplier:
Top-Quality Titanium Ground Bars from STA: For manufacturers seeking high-quality titanium ground bars to elevate engine performance, STA stands out as the preferred choice. As a leading titanium ground bar supplier, STA offers a diverse range of options, enabling manufacturers to explore the full potential of titanium in engine innovation.
To discover the myriad possibilities that titanium presents in advancing engine technology, contact STA today at [Your Contact Information].