Table of Contents
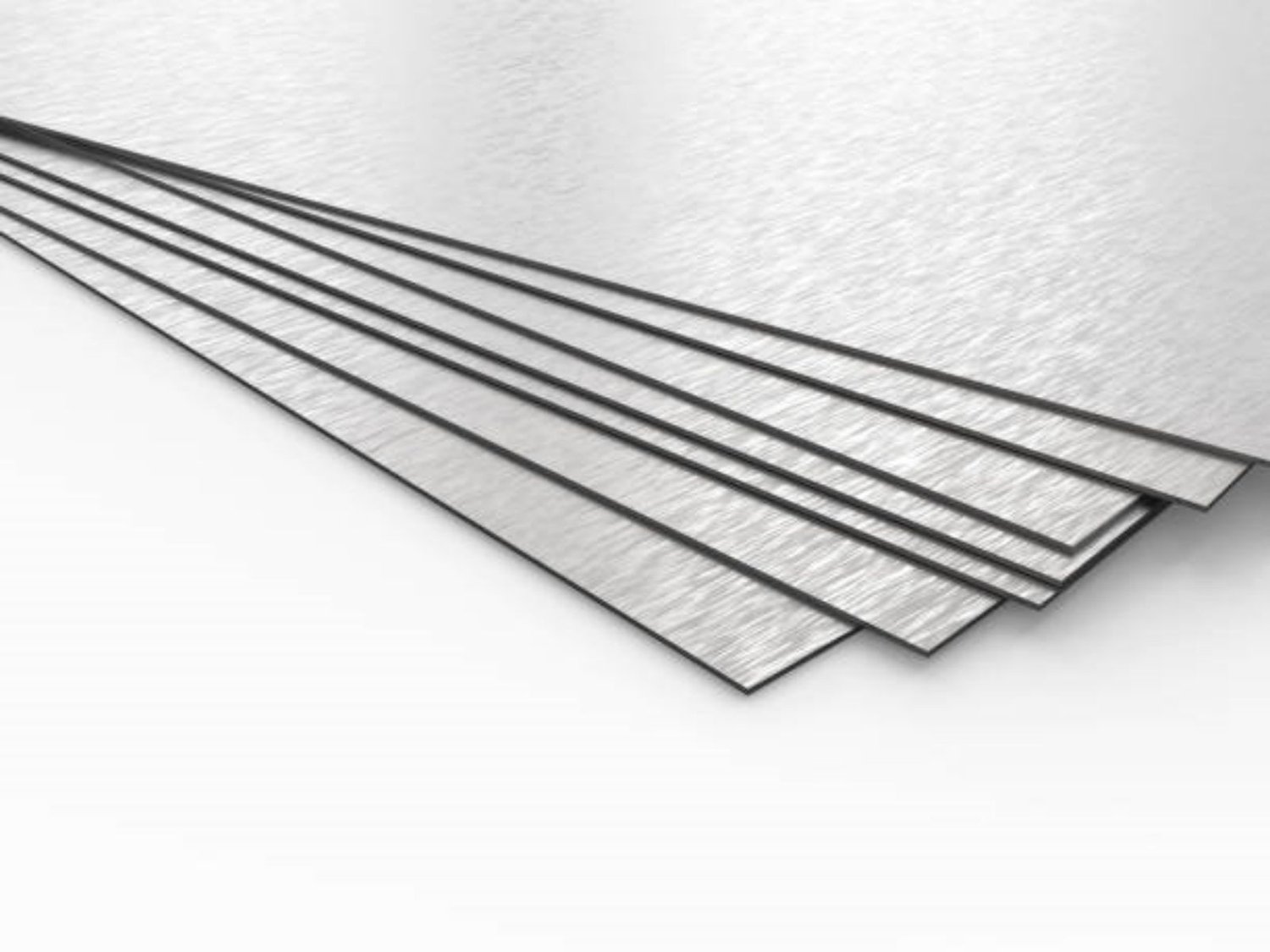
The Importance of Titanium Plates in Industrial Applications
Titanium plates are highly valued in various industrial sectors due to their exceptional properties and versatility. With excellent strength-to-weight ratio, corrosion resistance, and biocompatibility, titanium plates have become an essential material for aerospace, automotive, chemical, and medical industries. In this article, we will explore the process of manufacturing and processing titanium plates for industrial use.
Melting and Forming Titanium Ingots
The first step in processing titanium plates is the production of titanium ingots. These ingots are created through a process called the Kroll process or the Hunter process. In this process, titanium ore is combined with chlorine gas to form titanium tetrachloride, which is then reacted with magnesium or sodium to produce titanium sponge. The sponge is melted in a vacuum arc furnace and cast into ingots. These ingots are the starting point for further processing.
Hot and Cold Rolling
Once the titanium ingots are obtained, they are subjected to hot and cold rolling processes to reduce their thickness and achieve the desired dimensions. Hot rolling involves heating the ingots to high temperatures and passing them through a series of rollers. This process improves the mechanical properties of the titanium, making it more ductile and easier to work with. Cold rolling follows, where the titanium sheet is further reduced in thickness using room temperature rollers.
Heat Treatment and Annealing
After the rolling process, the titanium plates may undergo heat treatment to enhance their properties. Heat treatment involves heating the material to specific temperatures and then cooling it down in a controlled manner. This process helps relieve internal stresses, improve strength, and refine the microstructure of the titanium plates. Annealing, a specific type of heat treatment, is often performed to increase the material's ductility and reduce hardness.
Precision Cutting and Machining
Once the titanium plates have been rolled and heat-treated, they are ready for precision cutting and machining. This step involves using advanced cutting tools, such as water jets or lasers, to accurately shape the plates according to specific dimensions and designs. Machining processes, such as drilling, milling, and turning, may also be employed to create complex features or remove excess material.
Surface Finishing and Cleaning
Surface finishing plays a crucial role in titanium plate processing for industrial use. The plates may undergo processes like grinding, polishing, or blasting to achieve a desired surface texture or smoothness. Additionally, thorough cleaning is essential to remove any contaminants or impurities that may affect the material's performance. Ultrasonic cleaning or acid pickling are common methods used to ensure the plates are pristine before their industrial applications.
Quality Assurance and Testing
Before titanium plates are released for industrial use, they undergo rigorous quality assurance measures and testing. These include non-destructive testing techniques, such as ultrasonic testing, to detect any flaws or defects within the plates. Mechanical testing is also conducted to evaluate the material's strength, hardness, and impact resistance. Only after passing these tests are the titanium plates deemed suitable for industrial applications.
Surface Treatment and Coating
In certain industrial applications, titanium plates may require surface treatment or coating to enhance their performance or provide additional functionalities. Surface treatments, such as anodizing or passivation, can improve corrosion resistance, while coatings like ceramic or diamond-like carbon can enhance wear resistance. These treatments and coatings extend the lifespan and durability of titanium plates in challenging industrial environments.
Forming and Welding
Depending on the specific industrial application, titanium plates may need to undergo further forming or welding processes. Forming techniques, such as bending or deep drawing, allow the plates to be shaped into complex geometries or structures. Welding, using specialized techniques like gas tungsten arc welding (GTAW) or electron beam welding (EBW), is commonly employed to join titanium plates together and create larger components or assemblies.
Quality Control and Certification
Throughout the entire process of processing titanium plates for industrial use, quality control measures and certification play a crucial role. Adhering to strict quality control standards ensures that the final products meet the required specifications and performance expectations. Certification bodies, such as the International Organization for Standardization (ISO), provide certifications that validate the quality and consistency of titanium plates, giving customers confidence in their industrial applications.
Conclusion
The processing of titanium plates for industrial use involves a series of precise and controlled steps, starting from the production of titanium ingots to the final quality control and certification. By understanding and implementing these processes effectively, manufacturers can ensure the production of high-quality titanium plates that meet the demands of various industrial sectors. The exceptional properties of titanium plates make them a valuable material for countless industrial applications, contributing to technological advancements and innovation.