Table of Contents
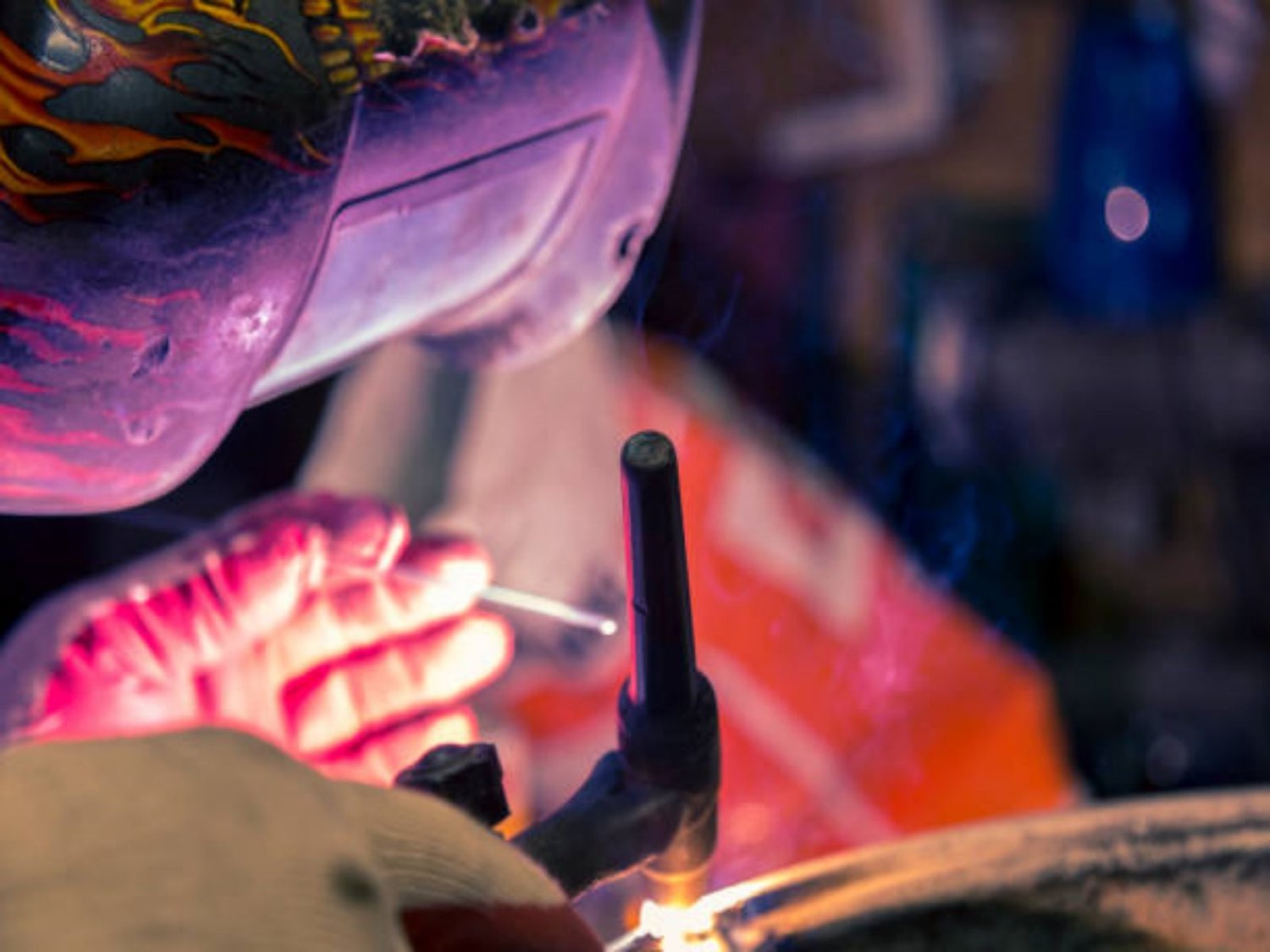
Understanding the Importance of High-Quality Titanium Tubes in Industrial Applications
When it comes to industrial applications, the quality of materials used plays a crucial role in determining the performance and reliability of the final product. One such material that is extensively used in various industries is titanium. Titanium offers exceptional strength, durability, and corrosion resistance, making it an ideal choice for applications where reliability is paramount. In this article, we will delve into the process of producing high-quality titanium tubes for industrial applications and explore the various factors that contribute to their success.
The Raw Material: Pure Titanium
The journey of producing high-quality titanium tubes begins with the selection of the right raw material. In this case, pure titanium, which is free from impurities, is the preferred choice. Pure titanium ensures the end product possesses the desired mechanical properties and can withstand the harsh operating conditions often encountered in industrial applications.
Melting and Alloying
Once the pure titanium is obtained, it undergoes a melting process. The titanium is heated to its melting point and carefully alloyed with other elements, such as aluminum or vanadium, to enhance its mechanical properties. This alloying process helps in improving the strength, ductility, and corrosion resistance of the final titanium tubes.
Tube Formation: Seamless or Welded?
After the alloying process, the titanium is ready to be transformed into tubes. There are two primary methods for tube formation: seamless and welded. Seamless titanium tubes are created by piercing a solid titanium billet and then extruding it through a die to form the desired tube shape. On the other hand, welded titanium tubes are created by rolling a titanium sheet into a tube shape and then welding the edges together. Both methods have their own advantages and are used based on the specific requirements of the industrial application.
Heat Treatment for Enhanced Properties
Heat treatment is a critical step in the production of high-quality titanium tubes. It involves subjecting the tubes to controlled heating and cooling processes to achieve specific microstructures and mechanical properties. Heat treatment helps in optimizing the strength, hardness, and flexibility of the titanium tubes, enabling them to withstand extreme conditions and perform reliably in industrial applications.
Precision Machining and Finishing
Once the titanium tubes have been formed and heat-treated, they undergo precision machining to achieve the desired dimensions and surface finish. Precision machining involves cutting, drilling, and shaping the tubes to meet the exact specifications required by the industrial application. The tubes are then carefully inspected for any defects or imperfections and undergo surface finishing processes, such as polishing or sandblasting, to ensure a smooth and uniform appearance.
Quality Control Measures
Producing high-quality titanium tubes for industrial applications requires stringent quality control measures. These measures involve extensive testing and inspection at various stages of the production process. Non-destructive testing techniques, such as ultrasonic testing and visual inspection, are employed to detect any internal or surface defects. Mechanical testing, such as tensile strength and hardness testing, is also conducted to ensure the tubes meet the required standards and specifications.
Surface Treatment: Protecting Against Corrosion
Industrial applications often expose titanium tubes to corrosive environments. To enhance their resistance to corrosion, surface treatment techniques are employed. One common method is through the application of a protective coating, such as a ceramic or polymer-based coating. These coatings act as a barrier, preventing corrosive substances from coming into direct contact with the titanium surface and prolonging the lifespan of the tubes.
Packaging and Transportation
Once the high-quality titanium tubes have undergone all the necessary processes, they are carefully packaged to ensure their protection during transportation. Special attention is given to prevent any damage or deformation that could compromise the integrity of the tubes. Proper packaging materials, such as wooden crates or foam padding, are used to provide cushioning and stability during transit.
Ongoing Research and Development
The production of high-quality titanium tubes for industrial applications is an ongoing process that involves continuous research and development. Manufacturers are constantly striving to improve the performance and efficiency of titanium tubes by exploring new alloying techniques, optimizing heat treatment processes, and developing innovative surface treatments. This commitment to innovation ensures that titanium tubes continue to meet the ever-evolving demands of industrial applications.