Table of Contents
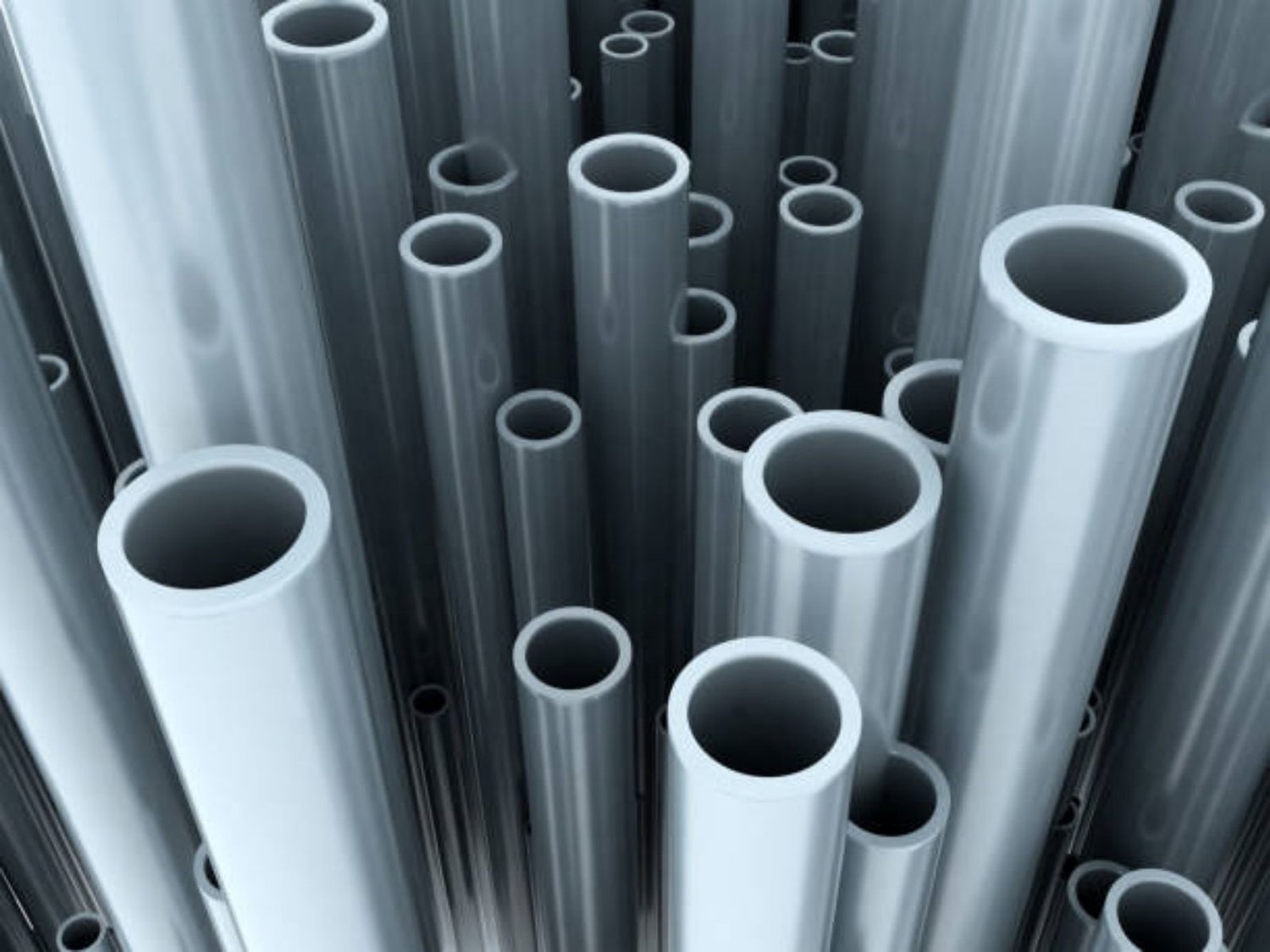
Enhancing Quality: Production Methods for High-Quality Titanium Tubes
When it comes to manufacturing titanium tubes, ensuring high-quality is of paramount importance. These tubes are widely used in various industries, including aerospace, automotive, and medical. In order to meet the rigorous demands of these sectors, manufacturers employ advanced production methods that guarantee the production of high-quality titanium tubes. In this article, we will explore ten different production methods that contribute to the creation of top-notch titanium tubes.
1. Precision Extrusion: Crafting Titanium Tubes with Precision
Precision extrusion is a production method that involves the controlled deformation of titanium billets through a die to create seamless tubes with precise dimensions. This method allows for the production of tubes with tight tolerances and excellent surface finish. By utilizing precision extrusion, manufacturers can achieve the desired mechanical properties and dimensional accuracy required for high-quality titanium tubes.
2. Seamless Rolling: Achieving Strength and Durability
Seamless rolling is a technique used to produce titanium tubes with exceptional strength and durability. This method involves the continuous rolling of heated titanium billets, which results in the formation of seamless tubes. Seamless rolling ensures a uniform grain structure, eliminating the weak points associated with welded tubes. This production method is highly favored in industries where strength and reliability are critical.
3. Hydroforming: Enhancing the Tube's Formability
Hydroforming is a production method that involves the use of fluid pressure to shape titanium tubes into complex geometries. By subjecting the tube to high-pressure fluid, hydroforming enhances its formability, allowing for the creation of intricate designs and shapes. This method is particularly useful in industries where lightweight components with complex forms are required, such as the aerospace industry.
4. Cold Pilgering: Achieving Uniform Wall Thickness
Cold pilgering is a cold-working process used to reduce the diameter and wall thickness of titanium tubes. This method involves the feeding of a titanium tube through a set of dies, which progressively reduce its dimensions. Cold pilgering ensures the uniformity of wall thickness throughout the tube, resulting in enhanced structural integrity and better dimensional accuracy. This production method is widely employed in the production of high-quality titanium tubes for critical applications.
5. Vacuum Arc Remelting: Purifying the Titanium Material
Vacuum arc remelting is a production method used to refine the titanium material by removing impurities and enhancing its microstructure. This process involves melting the titanium in a vacuum environment and then solidifying it to create a more homogeneous and purified material. By utilizing vacuum arc remelting, manufacturers can produce titanium tubes with improved mechanical properties, such as higher strength and fatigue resistance.
6. Hot Isostatic Pressing: Eliminating Porosity and Defects
Hot isostatic pressing (HIP) is a production method that involves the simultaneous application of heat and pressure to eliminate porosity and defects in titanium tubes. This process is carried out in a high-pressure gas environment, which allows for the uniform consolidation of the material. HIP is particularly beneficial for achieving a denser and more uniform microstructure, resulting in improved mechanical properties and reduced susceptibility to failure.
7. Electron Beam Welding: Creating Strong and Reliable Joints
Electron beam welding is a production method used to join titanium tubes together with high precision and strength. This welding technique utilizes a focused beam of electrons to melt and fuse the titanium material. Electron beam welding produces welds with minimal heat-affected zones, ensuring the integrity and strength of the joints. This method is widely employed in the production of high-quality titanium tubes where strong and reliable connections are essential.
8. Heat Treatment: Enhancing Mechanical Properties
Heat treatment is a crucial step in the production of high-quality titanium tubes. This process involves subjecting the tubes to controlled heating and cooling cycles to modify their microstructure and enhance their mechanical properties. By carefully controlling the temperature and duration of the heat treatment, manufacturers can achieve desired characteristics such as improved strength, hardness, and corrosion resistance.
9. Non-Destructive Testing: Ensuring Quality Assurance
Non-destructive testing (NDT) is an essential step in the production of high-quality titanium tubes. This method involves the use of various techniques to examine the tubes for any defects or imperfections without causing damage to the material. NDT techniques, such as ultrasonic testing and X-ray inspection, ensure the integrity and reliability of the tubes by detecting any hidden flaws that may compromise their performance.
10. Quality Control: Meeting Stringent Standards
Quality control plays a vital role in ensuring the production of high-quality titanium tubes. Manufacturers implement stringent quality control measures throughout the production process to monitor and assess the tubes' conformity to specified standards. This includes rigorous inspection, testing, and documentation of various parameters such as dimensions, mechanical properties, and surface finish. By adhering to strict quality control protocols, manufacturers can deliver titanium tubes that meet the highest industry standards.