Table of Contents
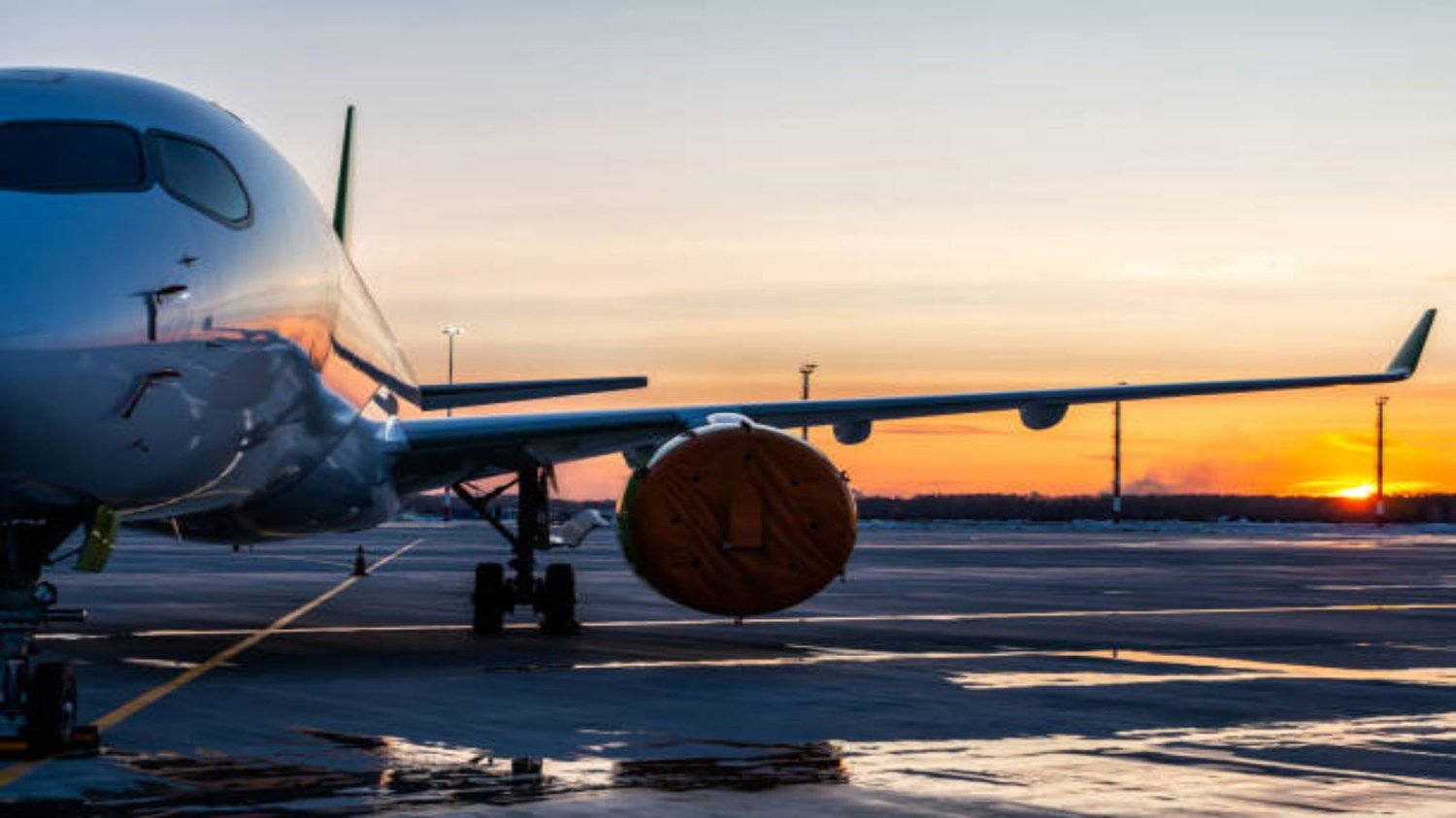
Choosing the Right Grade of Titanium Plate for Aerospace Components
Aerospace components require materials of the highest quality and strength to ensure reliable performance and safety. Titanium is one such material that has gained immense popularity in the aerospace industry due to its exceptional strength-to-weight ratio, corrosion resistance, and high-temperature capabilities. However, not all titanium plates are created equal. In this article, we will guide you on how to choose the right grade of titanium plate for your aerospace components, considering various factors that influence its suitability.
1. Understanding Titanium Grades
Titanium is available in various grades, each offering specific properties and characteristics. The most commonly used grades in aerospace applications include Grade 5 (Ti-6Al-4V), Grade 2 (Ti-CP), and Grade 23 (Ti-6Al-4V ELI). Grade 5 is the most widely used titanium alloy due to its excellent strength, while Grade 2 is commercially pure titanium known for its high ductility. Grade 23 is similar to Grade 5 but with reduced oxygen content, making it more suitable for biomedical applications.
2. Strength Requirements
When selecting a titanium plate for aerospace components, it is essential to consider the strength requirements. Aerospace applications often demand high strength-to-weight ratios to maximize fuel efficiency and performance. Grade 5 titanium offers the highest strength among commercially available titanium alloys, making it a popular choice for critical components such as turbine blades, engine components, and structural parts.
3. Corrosion Resistance
Aerospace components are exposed to harsh environments, including high humidity, temperature variations, and corrosive substances. Titanium is renowned for its exceptional corrosion resistance, especially against saltwater and various chemicals. Grade 2 titanium, being a commercially pure alloy, exhibits excellent resistance to corrosion and is frequently used in aerospace applications where corrosion resistance is critical.
4. Temperature Considerations
Another crucial factor to consider when choosing a titanium plate for aerospace components is its ability to withstand high temperatures. Aerospace engines and components operate under extreme conditions, and the material must retain its strength and integrity even at elevated temperatures. Grade 5 titanium possesses excellent high-temperature stability, making it suitable for applications where thermal resistance is essential.
5. Weldability and Fabrication
Weldability and fabrication characteristics play a significant role in the manufacturing process of aerospace components. Not all titanium grades exhibit the same ease of welding or fabrication. Grade 5 titanium, for instance, is known for its excellent weldability and machinability, making it ideal for complex aerospace component manufacturing. Grade 2 titanium, on the other hand, may require special welding techniques due to its higher purity.
6. Weight Considerations
Weight reduction is a critical factor in aerospace design, as it directly impacts fuel efficiency and overall performance. Titanium, being one of the lightest structural metals, offers a significant advantage in weight reduction compared to other materials. Grade 5 titanium's high strength-to-weight ratio makes it an excellent choice for aerospace applications where weight savings are crucial.
7. Cost Considerations
Cost is an important consideration in any manufacturing process. Titanium, being a premium material, can be more expensive than other metals commonly used in aerospace. The cost of titanium plates can vary based on the grade and the specific requirements of the aerospace component. It is essential to balance the desired properties with the available budget to ensure cost-effectiveness.
8. Quality Control and Certification
When choosing a titanium plate for aerospace components, it is crucial to ensure that the material meets industry standards and certifications. Quality control and certifications, such as those provided by the Aerospace Material Specification (AMS), help ensure the material's consistency, traceability, and reliability. It is recommended to source titanium plates from reputable suppliers who can provide the necessary certifications.
9. Application-Specific Considerations
Every aerospace component has unique requirements based on its intended application. For example, components exposed to extreme stress or fatigue may require a titanium plate with enhanced fatigue resistance properties, such as Grade 5 titanium with modified microstructures. Understanding the specific application requirements and consulting with materials engineers can help identify the most suitable titanium grade.
10. Long-Term Durability
Aerospace components are designed to operate for extended periods, and durability is a critical factor. The chosen titanium grade should exhibit long-term durability, with minimal degradation or loss of mechanical properties over time. Extensive research, testing, and analysis are conducted to ensure that titanium plates used in aerospace components can withstand the demanding conditions they are subjected to.