Table of Contents
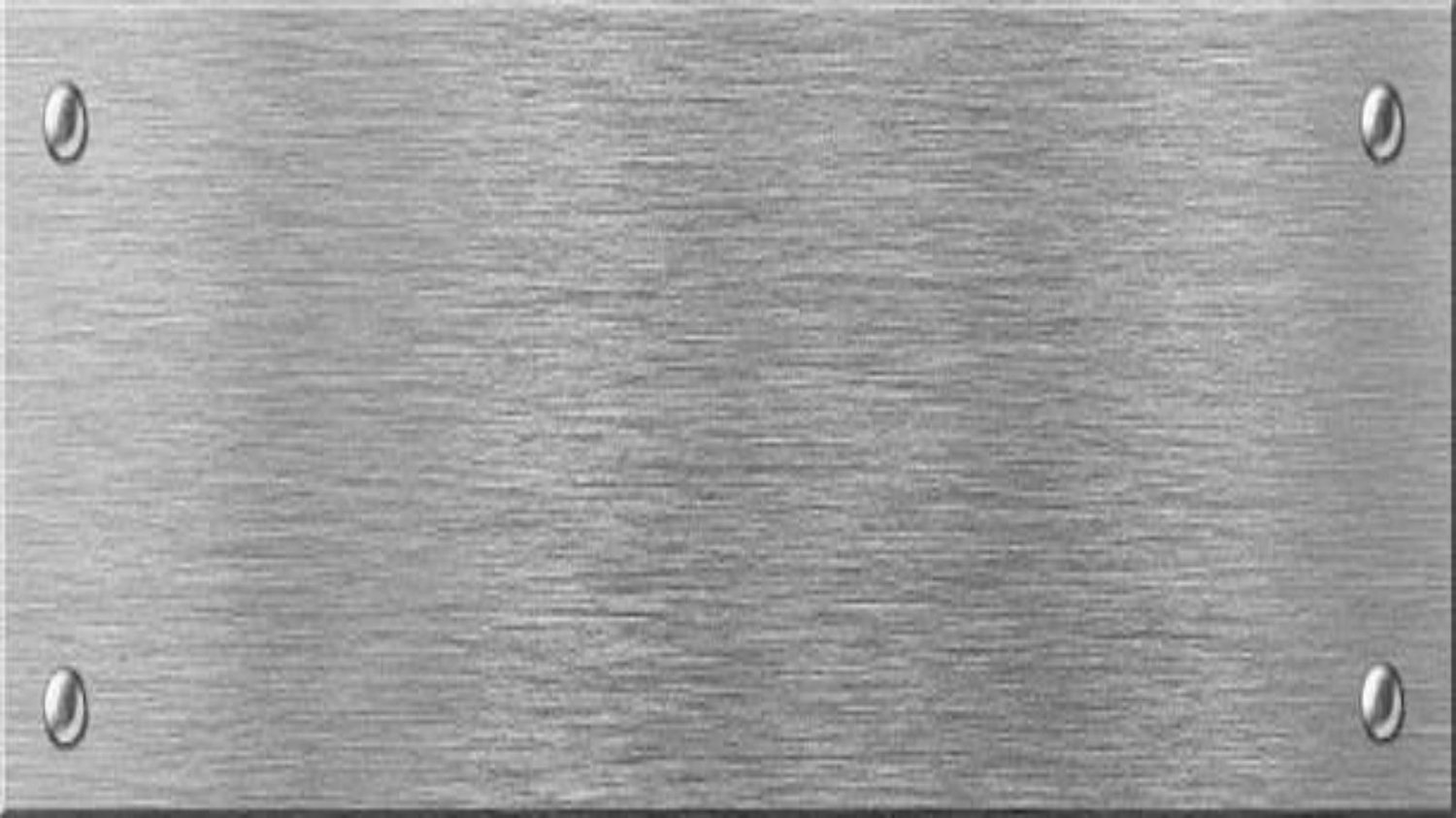
Understanding the Importance of Titanium Plate Thickness
Titanium is a versatile and highly sought-after material in various industries due to its exceptional strength, corrosion resistance, and lightweight nature. When it comes to titanium plates, choosing the right thickness is crucial to ensure optimal performance and durability in your specific application. In this article, we will explore the different titanium plate thickness options and help you determine what works best for your specific needs.
The Impact of Thickness on Strength and Weight
One of the primary considerations when selecting the appropriate titanium plate thickness is the impact it has on strength and weight. Generally, thicker plates offer higher strength and load-bearing capabilities. However, this also means increased weight, which may not be ideal for applications that require lightweight components. On the other hand, thinner plates are lighter but may sacrifice some strength and load-bearing capacity. It is essential to strike the right balance between strength and weight to ensure optimal performance.
Considerations for Corrosion Resistance
Another critical factor to consider when choosing titanium plate thickness is its corrosion resistance. Titanium exhibits excellent corrosion resistance in various environments, making it suitable for applications in industries such as aerospace, marine, and chemical processing. Thicker plates generally provide better corrosion resistance due to their increased surface area. However, thinner plates can still offer sufficient corrosion resistance if they are properly coated or treated with corrosion-resistant materials.
Thermal Expansion and Conductivity
Titanium plate thickness also affects its thermal expansion and conductivity properties. Thicker plates tend to have lower thermal expansion rates, making them more dimensionally stable when exposed to temperature changes. Additionally, thicker plates offer better heat dissipation and conductivity, which can be advantageous in applications that involve high temperatures or heat transfer. Thinner plates, on the other hand, may have higher thermal expansion rates and lower heat conductivity, which may impact performance in certain applications.
Impact on Machining and Fabrication
The chosen titanium plate thickness can significantly impact the ease of machining and fabrication processes. Thicker plates may require more machining time and effort, as they are harder to cut and shape. They may also require more robust machinery and tools. In contrast, thinner plates are generally easier to machine and fabricate, resulting in shorter production times and reduced costs. However, it is important to consider the specific requirements of your application and consult with experts to ensure the chosen thickness is suitable for your machining and fabrication needs.
Structural Considerations and Load-Bearing Capacity
When designing structures or components that require load-bearing capabilities, titanium plate thickness plays a critical role. Thicker plates are often preferred for applications that require higher strength and load-bearing capacity, such as aircraft frames, pressure vessels, and structural supports. Thinner plates, while lighter, may not provide the necessary structural integrity for such applications. It is crucial to carefully analyze the structural requirements of your application and choose a titanium plate thickness that can meet those demands.
Cost Considerations and Material Efficiency
Cost is another important consideration when selecting titanium plate thickness. Thicker plates generally cost more due to the increased material required and the additional machining and fabrication processes involved. Thinner plates, on the other hand, may offer cost savings, especially when large quantities are needed. Additionally, thinner plates can be more material-efficient, as they require less titanium. However, it is essential to balance cost considerations with the specific performance requirements of your application to ensure the optimal thickness is chosen.
Application-Specific Considerations
Each application has its unique requirements and constraints that must be taken into account when selecting the appropriate titanium plate thickness. For example, in aerospace applications, weight reduction is often crucial, so thinner plates may be preferred. In chemical processing applications, where corrosion resistance is paramount, thicker plates may be necessary. It is vital to thoroughly assess your application's specific needs and consult with experts who can provide guidance on the most suitable titanium plate thickness for your application.
Consulting with Experts
Given the complexity and importance of selecting the right titanium plate thickness, consulting with experts in the field is highly recommended. Experienced professionals can assess your application requirements, consider factors such as strength, weight, corrosion resistance, thermal properties, and fabrication needs, and provide valuable insights to help you make an informed decision. By leveraging their expertise, you can ensure that your chosen titanium plate thickness works best for your specific application.
Conclusion
Choosing the appropriate titanium plate thickness is crucial for the success and performance of your application. By considering factors such as strength, weight, corrosion resistance, thermal properties, fabrication needs, and cost considerations, you can determine the optimal thickness that works best for your specific requirements. Consulting with experts in the field ensures that you make an informed decision and leverage their expertise to achieve optimal results in your application.