Table of Contents
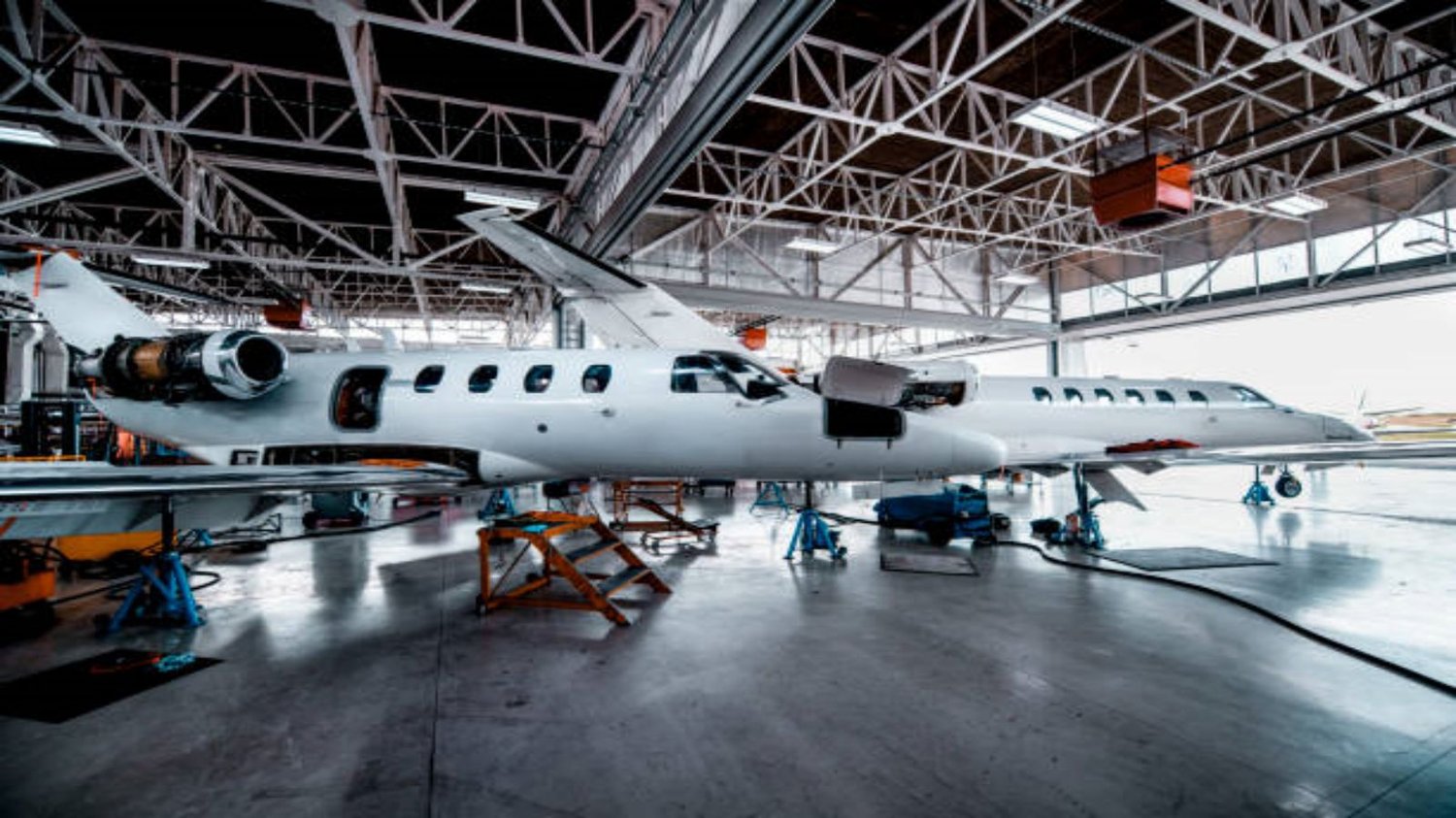
Titanium Tube Thickness Guidelines for Aerospace Manufacturing
When it comes to aerospace manufacturing, titanium tubes play a crucial role in ensuring the structural integrity and performance of various components. The selection of the appropriate tube thickness is of utmost importance to meet the stringent requirements of the aerospace industry. In this article, we will discuss the guidelines for titanium tube thickness in aerospace manufacturing, covering various aspects of this critical decision-making process.
1. Understanding the Importance of Titanium Tube Thickness
The thickness of a titanium tube directly impacts its strength, weight, and overall performance. In aerospace manufacturing, where weight reduction is a priority, selecting the right tube thickness is crucial for achieving the desired balance between structural integrity and weight savings. Moreover, the tube thickness also affects factors such as fatigue life, vibration resistance, and corrosion resistance.
2. Factors Influencing Titanium Tube Thickness Selection
Several factors come into play when determining the appropriate titanium tube thickness for aerospace applications. These factors include the intended use of the component, the operating conditions it will be subjected to, the type of load it will experience, and the specific regulations and standards imposed by the aerospace industry.
3. Regulatory Guidelines for Titanium Tube Thickness
The aerospace industry is highly regulated, and there are specific guidelines and standards in place to ensure the safety and reliability of aerospace components. Regulatory bodies such as the Federal Aviation Administration (FAA) and the European Aviation Safety Agency (EASA) provide guidelines on tube thickness requirements for various applications. Manufacturers must adhere to these guidelines to ensure compliance and meet the necessary certifications.
4. Structural Analysis and Finite Element Modeling
To determine the appropriate titanium tube thickness, structural analysis techniques, including finite element modeling (FEM), are employed. FEM allows engineers to simulate the behavior of the tube under different loads and conditions, enabling them to optimize the thickness for maximum performance. This analysis takes into account factors such as stress, strain, and buckling to ensure the tube can withstand the expected operating conditions.
5. Weight Optimization and Material Selection
Weight optimization is a critical consideration in aerospace manufacturing, as reducing weight directly translates to improved fuel efficiency and increased payload capacity. Titanium, known for its high strength-to-weight ratio, is a popular choice for aerospace applications. By carefully selecting the tube thickness, manufacturers can achieve the desired weight reduction while maintaining the necessary strength and structural integrity.
6. Fatigue Life and Durability
The fatigue life and durability of titanium tubes are essential factors in aerospace manufacturing. As components are subjected to cyclic loading during operation, the tube thickness must be selected to ensure adequate fatigue strength. Fatigue analysis, including techniques like fatigue crack growth analysis, is performed to determine the appropriate tube thickness that will provide the required durability over the expected lifespan of the component.
7. Vibration Resistance and Damping
Vibration resistance is another critical consideration in aerospace manufacturing. Titanium tubes with the correct thickness can effectively dampen vibrations, ensuring the overall stability and performance of the aircraft or spacecraft. By selecting the appropriate tube thickness, engineers can optimize the damping characteristics and minimize the risk of fatigue failure or resonance issues caused by excessive vibrations.
8. Corrosion Resistance and Environmental Factors
Aerospace components are exposed to various environmental factors, including high humidity, temperature fluctuations, and corrosive substances. Titanium is known for its excellent corrosion resistance, but the tube thickness also plays a role in protecting against corrosion. Thicker tubes provide an additional barrier against environmental elements, enhancing the overall corrosion resistance of the component and extending its service life.
9. Material Testing and Quality Control
Once the appropriate titanium tube thickness is determined, it is crucial to ensure the quality and integrity of the manufactured components. Material testing and quality control processes, including non-destructive testing (NDT) techniques such as ultrasonic testing and X-ray inspection, are employed to verify the tube thickness and detect any potential defects or imperfections that may compromise the performance and safety of the components.
10. Ongoing Research and Development
The aerospace industry is continuously evolving, with ongoing research and development efforts focused on improving the performance and efficiency of aerospace components. This includes advancements in materials, manufacturing processes, and design optimization techniques. As such, the guidelines for titanium tube thickness in aerospace manufacturing are subject to updates and refinements as new technologies and insights emerge.